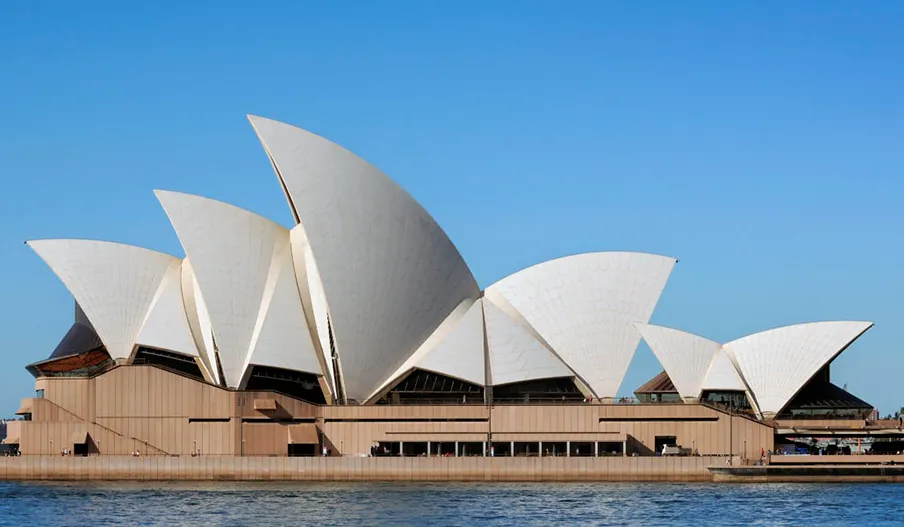
Бетон
Бетон — искусственный каменный строительный материал, получаемый в результате затвердевания рационально подобранной, тщательно перемешанной и уплотнённой смеси из минерального или органического вяжущего вещества, крупного или мелкого заполнителей, воды. В ряде случаев может имет в составе специальные добавки, а также не содержит воду (например, асфальтобетон). Бетон и железобетон являются самыми популярными материалами, применяемыми в строительстве на территории России и СНГ.
В домостроении наиболее широко используют бетоны, изготовленные на цементах. Цемент и вода являются активными составляющими бетона, в результате их реакции образуется цементный камень который скрепляет зёрна заполнителя в монолит. Набравший прочность бетон обеспечивает лучшую устойчивость чем любой другой строительный материал к сильному ветру, урагану или торнадо благодаря своей жесткости, которая приводит к минимальному горизонтальному перемещению. Особое расположение бетонных элементов и схемы армирования, делают здания и сооружения чрезвычайно прочными, как например, в случае SCIP.
ИСТОРИЯ БЕТОНА
Наиболее ранний из сохранившегося бетона обнаружен при раскопках древнего поселения Лепенски Вир (Сербия), считается он был уложен в 5600 г. до н.э. — в одной из хижин был изготовлен пол толщиной 25 см из бетона замешанного на гравии и местной красной извести в качестве цемента.
Первыми крупными потребителями бетона были древние египтяне (2500 г. до н.э.) — они использовали глину смешанную с соломой для скрепления каменных глыб. Позже римляне, начиная с 300 г. до н.э., внесли множество изменений в технологию бетона, включая использование гашеной извести и вулканического пепла (пуццулана), что позволяло им делать гидробетон, застывающий в воде. Римляне использовали бетон в массовом строительстве общественных зданий и сооружений, включая Пантеон, его купол до сих пор остается самым большим в мире куполом из неармированного бетона (диаметр 43,3 м). Взгляните на грандиозные римские бани и амфитеатры, и вы оцените преимущества бетонного строительства. После 400 г. н.э., с завоеванием Рима варварами искусство бетона было утрачено.
Подробную хронологию начала современной истории бетона можно почитать в книге Роберта Курланд «Бетонная планета». Если кратко, то в 16 веке жители г. Андернаха (Германия) обнаружили магматический камень, который идеально подходит для строительных целей, а в измельчённом виде, является идеальной пуццоланой для изготовления бетона. Местные его назвали «Трасс». О нём упоминает своей книге «Архитектура и гидравлика» (1748) французский инженер Бернар Форест.
Затем были открытия британского инженера Джона Смитона (1724-1792), его эксперименты на известковых растворах послужили поворотным моментом в истории строительства, люди по всей Англии будут продолжать экспериментировать с различными смесями и технологиями производства с целью создания цемента лучшего качества. Началась регистрация патентов: Б. Хиггинс (1779), Джеймс Паркер (1791, 1796), в конце-концов появляется фирма «Фрэнсис и Уайт», которая станет одним из самых успешных производителей роман цемента в Англии. Ключевой патент на портландцемент («искусственный камень»), который до сих пор остается ключевым компонентом бетона, зарегистрировал в 1824 году Джозеф Аспдин.
ПЕРВЫЙ БЕТОННЫЙ ДОМ
Последующие разработки материалов, более высокая температура обжига, вращающаяся печь непрерывного действия и т. д. значительно улучшили материал и снизили стоимость. С 1835 года велось строительство нескольких зданий для Джона Уайта в Суонскомбе (Кент, Англия), стены, плитка, оконные рамы и декоративные детали которых были выполнены из бетона. При проектировке специально старались добиться его похожести на любой другой викторианский дом [ 1 ].
Сталь
Сталь впервые в гражданском строительстве стали массово использовать в Англии, в 1860-70-х гг. Сварная сетка появилась в конце Первой мировой войны, металлическая скрученная намного раньше.
Ферроцемент, железобетон
Но концепция армирования материала вряд ли существовала в этот период. Чтобы преодолеть низкую прочность бетона на растяжение, были предприняты попытки его армирования с помощью бронзовых стержней и полос. Но более высокая скорость теплового расширения бронзы вызвала растрескивание.
В 1802 году при строительстве Царскосельского дворца российские зодчие использовали металлические стержни для армирования перекрытия, выполненного из известкового бетона. 18.01.1825 г. открылся Большой театр в Москве, его фундамент был укреплен с использованием более 10 тыс. м³ бетона — создана железобетонная монолитная фундаментная плита, а также установлены плиты перекрытий под землёй.
В 1829 году английский инженер Фокс реализовал армированное металлом бетонное перекрытие. Марк Брюнель в 1830-х годах провел ряд важных экспериментов по железобетонной кладке с использованием железных обручей для бочек и римского цемента, доказав, что прочность на растяжение таких конструкций значительно улучшилась. Уильям Уилкинсон, строитель нового замка, в 1854 году получил патент на встраивание в перекрытия или бетонные балки сети плоских железных стержней (John E Morgan 1998).
Совместная работа стального армирования и бетона, позволяет готовому изделию успешно выдерживать высокие нагрузки, обеспечивать прочность и долговечность зданий и сооружений. Железобетон имеет преимущество перед стальным каркасом: это гибридный материал сочетающий в себе прочность бетона на сжатие, с замечательной прочностью стали на растяжение. Вследствие этого, требовалось меньше стали, а следовательно и расходы на строительство сокращались. Чем выше прочность арматуры и бетона, тем меньше их расход, тем эффективней и экономичней возведенные из него объекты. Сегодня по монолитной технологии строят 94% высотных зданий.
В 1848 году Жозеф-Луи Ламбо французский садовод, живший в своем поместье в Миравале недалеко от Брингноля в Варе, экспериментировали с горшками для растений, сиденьями и ваннами, сделанными из тонкой проволочной сетки и обмазанными песком и цементным раствором, заменяя его гниющую гребную лодку. Он назвал этот материал «Ferciment» в патенте, который он получил в 1852 году. В 1854 года посетители Всемирной парижской выставки на озере Мираваль обращали внимание на бетонную весельную лодку, она служила прогулочным судном в парижских парках и воспринималась как чудо техники до самого конца 19 века. Ламбо первым ввёл применение армоцемента в области гражданского строительства, его весельные лодки до сих пор находятся в музее Бриньоля во Франции.
Ферроцемент (армоцемент) представляет собой форму армированного бетона, которая отличается от обычного армированного или предварительно напряженного бетона прежде всего способом распределения и расположения армирующих элементов. Он состоит из нескольких близко расположенных слоев сетки или тонких стержней, полностью залитых цементным раствором. Образуется композиционный материал, который ведет себя иначе, чем обычный железобетон, по прочности, деформации и потенциальным применениям, и поэтому классифицируется как отдельный и отличный материал. Он может быть сформирован в виде тонких панелей или секций, в основном толщиной менее 1 дюйма (25 мм), только с тонким слоем раствора поверх самых внешних слоев арматуры. Как и в случае обычного бетона, арматуре из ферроцемента можно придать желаемую окончательную форму, а раствор затереть непосредственно на месте без использования опалубочной формы. [ 2 ].
Подробнее о ферроцементе (армоцементе) ниже, сейчас же отметим, что технологии того времени не могли обеспечить строительство большим объемом проволоки, необходимой для изготовления сетки. Вместо этого для изготовления того, что сейчас называют стандартным железобетоном, использовались большие арматурные стержни, а концепция армоцемента была почти забыта на 100 лет. Так, получил развитие привычный сегодня железобетон в достаточно массивных конструкциях, материал, для создания которого опалубка удерживает свежий бетон в широких зазорах между арматурными стержнями и достаточно толстым слоем.
С первыми попытками железобетонного строительства часто связывают имя Коанье, его конструкции датируют около 1860 г. В этих 1860-х годах, парижский садовник Жозеф Монье экспериментировал с цементным раствором для изготовления цветочных кадок, которые могли бы заменить деревянные. Сперва он изготавливал их только из песка и цемента, но кадки получались очень тяжелыми, перемещать их было неудобно. Тогда Монье поставил себе новую задачу, — добиться такого способа изготовления кадок, при котором хорошие свойства цементных кадок, их прочность и выносливость, как против повреждения, так и против гнили, сочетались бы с небольшим весом. Самостоятельно ли, или опираясь на упомянутые образцы других изобретателей железобетона, он решил эту задачу, покрыв железную проволочную сетку цементным раствором. Решетка из сравнительно тонкой проволоки придавала отвердевшему раствору такую прочность, что прежняя толщина стенок и вместе с тем собственный вес могли быть значительно уменьшены. То есть фактически слой ж/б панели SCIP был придуман Монье ещё в 1860-х.
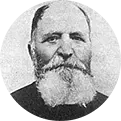
Сначала Жозеф создал опалубку (вставил одну кадку во вторую с бо́льшим диаметром), затем залил промежуток цементным раствором. Так как и эти кадки были ещё слишком хрупкими, он вставил кадку в каркас из железной проволоки и для красоты замазал каркас цементным раствором. После затвердения получилась кадка удивительной прочности. В 1867 получил патент на свою укреплённую садовую кадку, продолжил эксперименты, получил ряд патентов в смежных областях: укреплённые железом цементные трубы и бассейны (1868), железоцементные панели для фасадов домов (1869), мосты из железоцемента (1873), железобетонные балки (1878). Источник
Достоверно известно, что американец Гиат уже в 1865 г. производил опыты с железобетонными балками. Томас Эдисон, тот самый имя которого связывают с телефоном, телеграфом, электрической лампой и фонографом, основал Edison Portland Cement Co., которой внёс значительные усовершенствования в процесс производства цемента.
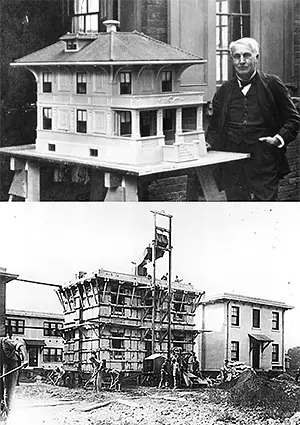
Эдисон опередил своё время, полагая, что бетон будет иметь широкий спектр применения. Он представлял себе будущее с бетонными домами заполненными бетонной мебелью и холодильниками (тепловая масса). С Генри Фиппс-младшим они увидели потенциал этих доступных домов и считали их решением проблемы трущоб и нехватки жилья в Нью-Йорке. Они хотели построить целый город, где бы семьи рабочего класса имели относительно недорогой, прочный, пожаробезопасный дом. Цена монолитного дома с трубопроводом, ванной и другими удобствами составляла около $1200, что было в 3 раза дешевле кирпичного дома. Проект не взлетел из-за недостатка финансирования и незаинтересованности подрядчиков. В 1922 году компания построила знаменитый стадион «Янки» (Нью-Йорк), который служил домом для «Нью-Йорк Янкиз» до 2008 г., и вскоре пала жертвой Великой депрессии в США.
В квартирном строительстве кирпич уже не используют, из малоэтажного он также уходит. Например, в пристанище миллионеров на о. Пальма в Дубае, у всех домов ж\б каркасы, кирпича нет, ну чем не свидетельство?
Первые монолитные дома появились в Москве ещё в 30-е гг. прошлого столетия, в период конструктивизма. Кстати, одно из красивейших зданий Киева «Дом с Химерами» (1902), было построено архитектором Городецким именно с целью рекламы и продвижения бетона в строительство. Но в СССР, в основном, строили сборным железобетоном (см. ниже), монолитный способ получил развитие где-то к 1990-м гг. В те годы СП для него не существовало, текущие нормативы просто перенесли из проектирования зданий из сборного железобетона, хотя в действительносш поведение монолита и ОКБ очень отличается.
Знаменитые хайвэи в США покрыты бетоном — 55 000 миль шоссе залиты высококачественным, не боящимся влаги и мороза бетоном. Первая бетонная дорога была уложена в 1913 г. в штате Арканзас. Мостовые и дороги из бетона служат до 20-30 лет без капремонта, в то время как асфальтированные всего 8-12 лет, и то, если их правильно уложить (на 40 см подушке и с идеальной плоскостностью).
Несмотря на очевидные преимущества бетона, его высокой прочности на сжатие, сопротивление ветру, огнестойкости, универсальности, пластичности, теплоёмкости, долговечности, низких расходах на эксплуатацию, звукоизоляции, нетоксичности — исторически, в строительстве малоэтажного жилья бетон всё же применялся ограниченно. Сегодня применение этого древнейшего строительного материала быстро растет во всем мире, он уже является наиболее применяемым строительным материалом современности, этот искусственный материал широко используется при строительстве зданий любого типа.
Исследования и разработки ученых, в том числе в области нанотехнологии, дают основания полагать, что бетон не уступит своих лидирующих позиций и в ближайшем будущем. Уже появились биобетон, гибкий бетон (ECC) светопрозрачный бетон и др. Лучшие образцы модифицированного бетона уже сегодня почти в 3 раза превосходят по компрессионной прочности стандартный бетон образца начала 1970-х гг., что в т. ч. позволяет в промышленных масштабах создавать куда более тонкие, легкие и протяжённые железобетонные конструкции.
Специалисты одного из наиболее крупного исследовательского центра Concrete Sustainability Hub (CSHub) при Массачусетском Технологическом Институте (MIT) в Бостоне (США), впервые в мире смогли точно искусственно смоделировать структуру бетона на атомарном уровне, что позволило им найти ряд эффективных методов создания более прочных, долговечных и экологичных бетонов, и выявить ключевые механизмы последующего целенаправленного изменения его различных свойств и практического назначения. «Мы создали первую модель структуры бетона в атомном масштабе» говорит Р. Пелленк, директор лаборатории MIT-CNRS
ПРЕИМУЩЕСТВА МОНОЛИТНОГО ДОМОСТРОЕНИЯ
Среди основных преимуществ монолитного домостроения:
- Замкнутый цикл, позволяющий производить основной материал строительства на бетоносмесительном оборудовании прямо на стройплощадке.
- Возможность любого архитектурного решения; гибкая, свободная планировка; индивидуальность здания.
- Самая высокая несущая конструкционная способность зданий и сооружений при относительно тонких стенах.
- Высокая точность и скорость изготовления достигается использованием современного оборудования.
- Практически неограниченное время службы конструкций при условии их защиты от атмосферных разрушающих факторов.
- Не требует дополнительной отделки, в то время как кирпичная стена нуждается в штукатурке, что дополнительная нагрузка на фундамент, время и затраты.
Однако доступ к этой технологии преграждает стоимость опалубки и затраты связанные с её использованием на строительной площадке, транспортировкой и хранением; а так же вложения в бетоносмесительное и насосное оборудование, что могут позволить только крупные застройщики.
Новые высокоэффективные монолитные технологии используют как традиционные преимущества бетона, так и новые. Например, для SCIP не нужна опалубка. Бетонные сэндвич-панели с новыми средствами армирования, позволяют получить более лёгкие и тонкие слои бетона, конструкции меньше весят, имеют более высокое теплосопротивление, выше экономичность, их скорость строительства выше, выше устойчивость к землетрясениям, водостойкость, гибкость дизайна, они могут иметь более привлекательную отделку, строительство становится всепогодным, ниже требования к навыкам и др. Подробнее.
Сетчатые конструкции Шухова
Выдающийся российский инженер и архитектор В.Г.Шухов был изобретателем стальных конструкций в мире, это он впервые в архитектуре использовал стальные сетчатые оболочки с несущей решёткой (1896 г). Он не только знал и понимал как работают конструкции, он чувствовал как в силовых элементах распределяются усилия и перетекают напряжения. Максимально сокращая количество ступеней в передаче нагрузки элементами пространственно работающего перекрытия, более 100 лет назад он отказался от четырехступенчатых покрытий (кровля, обрешетка, прогоны, фермы), о которых только недавно заговорили, что они так же «экономичны», как действия 4-х человек переносящих рояль, которые забрались друг-другу на плечи и дали рояль верхнему.
Владимир Григорьевич первым подошел к конструктивной форме с научных позиций: после функциональности его главные критерии: вес, трудоёмкость и стоимость. Именно эти критерии явились основополагающими, например, при создании им в 1895-96 гг. павильонов для Всероссийской промышленной и художественной выставки в Нижнем Новгороде. Сетчатые конструкции главного павильона выставки и покрытия двоякой положительной и отрицательной Гауссовой кривизны были исключительно оригинальны и блестяще решали проблему минимального веса.
Поразившие всех посетителей выставки и специалистов сетчатые оболочки В.Г. Шухова вызвали горячие споры, но никто не сомневался, что дано решение принципиально новыми средствами проблемы наиболее эффективной работы материала в конструкции и практически обеспечено резкое снижение на этой основе весовых (в 3 раза и более) и других экономических показателей. Эти новаторские конструктивные решения только через несколько десятилетий проложили себе дорогу в мировой строительной практике — знаменитые архитекторы Норман Фостер (его центр визуальных искусств в Сэйнсбери весит всего 5619 тонн, в то время как Эмпайр Стейт Билдинг 370 тысяч тонн) и Бакминстер Фуллер, окончательно внедрили сетчатые оболочки в современную практику строительства. Тонкостенные пространственные конструкции добиваются большего путём самоограничений, они стали вершиной успехов строительной техники ХХ века, одним из главных средств формообразования авангардных зданий.
Первое повторение сетчатых конструкций Шухова было сделано только в 1932 году в Олбани (США). Но полное признание и широкое распространение в прогрессивной архитектуре сетчатые оболочки получают только в течение последних двух десятилетий. Благодаря появлению новых строительных материалов и технологий, внедрению компьютеров в практику расчёта конструкций — сетчатые оболочки становятся одним из главных средств формообразования авангардных зданий, включая небоскрёбы и шедевры стиля «hi-tech». Например, в Гуанчжоу (Китай) построена самая высокая телебашня в мире, 650 метров, по шуховскому принципу. Китайцы с гордостью говорят о том, что они продолжатели традиций Шухова. В Дохе (Арабские Эмираты) 400-метровая башня тоже построена по его принципу.
Сетчатые несущие оболочки постепенно вытесняют из строительной практики ж/б несущие оболочки с периодической арматурой, ряд аварий заставляет задуматься над их эффективностью (Басманный рынок, аквапарк «Трансвааль» и др). Стальные сетчатые оболочки зданий и сооружений эксплуатируются в российском климате безаварийно, сетчатые оболочки Шухова без современной защиты не разрушаются от коррозии 80-110 лет.
Владимир Григорьевич Шухов (1853-1939) — принадлежит к блистательной плеяде отечественных ученых-инженеров, опередивших свое время. Уже при жизни современники его называли российским Эдисоном, первым инженером Российской империи и человеком-фабрикой. Диапазон его творчества огромен, главное его достижение — решение непрерывного крекинга нефти, благодаря чему Россия получила приоритет в этой области. Также Шухов спроектировал нефтеналивные баржи, которые ходили по Волге (причем эти принципы до сих пор используются в современных танкерах). Он был основоположником теории расчета резервуаров для хранения нефти. Арабские Эмираты, США, Россия — везде цилиндры патентованные Шуховым. За свою жизнь он спроектировал и построил тысячи промышленных корпусов, всевозможных перекрытий, сотни мостов, десятки гигантских для того времени резервуаров, газгольдеров, огромное количество наливных барж, сотни гиперболоидальных опор водонапорных башен, маяков, кессоны для мостовых опор, водопроводы и многое другое. В Москве на Тургеневской площадив 2008 был открыт памятник инженеру Шухову. Первый в России.
Армоцементные конструкции Нерви
В 1943 году, на тот момент уже известный своей системой сборных большепролётных сводов из ромбовидных железобетонных звеньев, 52-х летний итальянский инженер и архитектор Пьер Луиджи Нерви (1891-1979) приступает к экспериментальным исследованиям армоцементных конструкций и получает патент под названием «ферроцемент» (железоцемент, армоцемент используется как синоним). Уже с 1943 года его начинают применять в судостроении Италии, а затем и в других странах.
Годами позже, создавая тонкие криволинейные оболочки для стадионов, концертных и выставочных залов и др. без использования традиционной деревянной опалубки (ее было очень сложно использовать для таких поверхностей) Нерви уже эффективно применял армоцемент без какой-либо опалубки. Эта идея обеспечила новому материалу триумф в мире и принесла Нерви славу «поэта железобетона».
Новый материал устранял все известные недостатки цементного камня: хрупкий и непрочный при растяжении, изгибе и ударе, но армированный несколькими слоями стальной сетки (армоцемент) — он создает упругий, трещиноустойчивый материал, обладающий высокой прочностью при действии всех видов нагрузок, в том числе удара, изгиба, растяжения. Несмотря на то что армоцемент как и железобетон состоит из бетона и стали, их свойства далеко не одинаковы. Главная особенность армоцементных конструкций в значительном увеличении поверхности сцепления арматуры (сетки) с бетоном, что позволяет конструкции выдерживать большие упругие деформации.
ЧТО ТАКОЕ АРМОЦЕМЕНТ
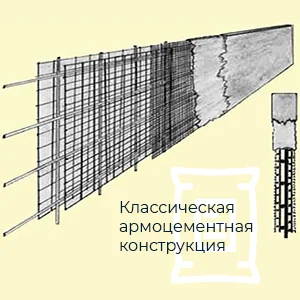
Это специальный слоистый композит на мелкозернистом цементно-песчаном бетоне марок повышенной плотности (М300—400), на заполнителе не крупнее 3 мм, в массе которого равномерно распределены тканые или сварные стальные сетки из тонкой проволоки, часто диаметром 0,5—1 мм с ячейками размером до 10х10 мм. Проволочные сетки равномерно распределены между собой, расстояние между ними 3-5 мм. Это позволяет получать достаточно однородный по свойствам материал. Может одновременно содержать стержневую или проволочную арматуру.
«В ферроцементе используются различные типы сеток, такие как шестиугольная проволочная сетка, сварная проволочная сетка, тканая проволочная сетка, просечно-вытяжная сетка и трехмерные сетки (three dimensional, 3D). Желаемая форма может быть построена из многослойной конструкции из мелкоячеистой сетки и, при необходимости, усилена стальной проволокой или стальными стержнями. Поверх этого готового каркаса наносится соответствующая смесь цемента, песка и воды. Во время затвердевания ферроцемент поддерживают во влажном состоянии, чтобы цемент мог схватиться и затвердеть». [ 3 ]
Способность бетона воспринимать растягивающие напряжения тем больше, чем больше поверхность сцепления арматуры с бетоном. Например, для получения армоцемента с повышенной упругостью и растяжимостью без образования трещин необходимо чтобы количество проволочных сеток составляло не менее 400-500 кг на 1 м³ бетона (по данным Нерви) или не менее 300 кг по данным исследований отечественных НИИ (содержание стали в конструкции SCIP обычно 190-230 кг/м³). B результате бетон более равномерно вовлекается в работу: снижается концентрация напряжений, более равномерно распределяются внутренние усилия, вследствие чего растяжимость армоцемента по сравнению с железобетоном увеличивается в 5 раз и более.
Чем гуще и равномернее расположена арматура, и тоньше проволока арматурных сеток, тем выше прочность и упругость сцепления арматуры с бетоном. Такое армирование определяет высокое сопротивление сечения трещинообразованию, водопроницаемости и местным ударным нагрузкам.
Морозостойкость армоцемента, как правило, превышает 100 циклов (Мрз < 100 циклов). Водонепроницаемость армоцементых конструкций также высокая, НИИСельстрой СССР проводил испытания армоцемента толщиной 20 мм на давление 16 атм с положительными результатами. Прочность на 10-15 % выше конструкций обычного бетона. Напряжения в проволоке при разрушении достигают 2500—2700 кг/см². Армоцементные конструкции имеют значительно большую ползучесть, чем обычные железобетонные. Исследования показывают, что для сжатых образцов при нагрузках 0,25-0,3 разрушающих деформации через год в 3 раза превышали кратковременные. Объемный вес армоцемента 2,5-2,8 г/м³ (при расчетах принимается 2,5 т/м³ при двух сетках и по 50 кг/м³ на каждую дополнительную сетку). Расход цемента от 400 до 800 кг/м³. Фракция частиц песка должна быть не более 5 мм; В/Ц — в пределах 0,25-0,28. По сравнению с железобетонными конструкциями армоцементные не требуют общего увеличения расхода цемента и стали на сооружение, так как объем армоцементных конструкций в 3-4 раза меньше.
В высотном строительстве в-основном конкурируют 2 концепции: сталь+стекло против железобетона, по крайней мере так себе определяют конкурента крупнейшие цементные корпорации в своих стратегических документах (автор знает о чём говорит). Производители стали указывают на то, что прочность бетона в среднем в 10 раз меньше прочности стали, что в больших конструкциях железобетон «несёт» больше своей массы, чем полезной нагрузки. Но с ферроцементом ситуация иная, его прочность выше обычного железобетона и его нужно меньше.
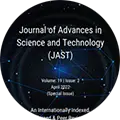
«Потребность в количестве ферроцемента при строительстве зданий намного меньше по сравнению с ЖБИ. Поэтому собственная нагрузка здания из ферроцемента снижается как минимум в 50 раз. Следовательно, снижается стоимость фундамента». [ 3 ]
ИСПОЛЬЗОВАНИЕ АРМОЦЕМЕНТА
Мы привыкли к железобетону в виде массивных конструкций, и впечатление от него остается как о материале очень сложном. Но армоцемент имеет почти такой же удельный вес, как и алюминий.
По объемному весу бетоны разделяются на лёгкие и тяжелые. Самый тяжелый судостроительный бетон легче алюминия: объемный вес тяжелых конструкционных бетонов составляет 1,8-2,2 т/м³ (например, модифицированный песчаный бетон который (по необходимости) мы применяем в SCIP SOTA, имеет удельный вес 2,0-2,4 т/м³), а для алюминия эта величина достигает 2,5 т/м³. Даже плотно армированный стальной арматурой железобетон (армоцемент) имеет почти такой же удельный вес, как и «крылатый металл»: — не более 2,7 т/м³. Для сравнения, сталь — 7,8 т/м³.
Армоцемент (ферроцемент) — прочный, универсальный, лёгкий, долговечный строительный материал, простой по составу, не требующий опалубки, трудоёмкий с минимальными навыками и низкой себестоимостью строительства. Его структура намного тоньше и легче обычного железобетона, состоит из тесно, но равномерно распределенных слоев проволочной сетки, которые обеспечивают большую прочность на растяжение, гибкость и лучшую устойчивость к растрескиванию, чем обычный бетон. Он устойчив к огню. Сырьё для его изготовления доступно в любом уголке мира, он легко изготавливается и формуется (можно придать любую форму).
Традиционные применения ферроцемента многочисленны и охватывают морские применения (лодки, понтоны и т. д.), наземные применения: резервуары для воды, силосы, бассейны, канализационные желобы, септики, можно использовать в качестве оборудования для пищевой промышленности, для продовольственных складов, газовых баллонов (для жидкого и природного газа), водонапорных башен.
Применяют и в гражданском строительстве (крыши, стены зданий, перекрытия), и для создания малых художественных форм различных строительных компонентов (козырьки, арки, скульптуры и др.), а также вспомогательные применения, такие как ремонт и восстановление, например, восстановление первоначальной прочности повреждённых железобетонных плит, балок и колонн лоскутным ремонтом или методом заплатки из ферроцемента.
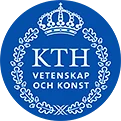
«Использование формы оболочки, которая естественным образом вызывает сжатие бетона, является ключевой частью проектирования с использованием ферроцемента. Особенно хорошо подходят такие формы, как купола и контактные балки. Однако более сложные оболочки очень трудно анализировать вручную, и поэтому компьютерный инструмент, такой как анализ методом конечных элементов (FEA), позволяет создавать сложные конструкции» — объясняет защитивший диссертацию на тему энергопассивных домов на основе ферроцемента, доктор Королевского Технологического Института Швеции Ян Луговский [ 4 ].
Использование высокоэффективных цементных матриц и высококачественных стальных сеток в сочетании с волокнами открывает возможности для новых применений, таких как защитные панели от снарядов (пуленепробиваемые панели) и взрывостойкие мембраны. Особенно его применение целесообразно для тонкостенных пространственных конструкций (с толщиной стенок 10—30 мм), и по сравнению с железобетоном значительно более лёгких изделий (оболочки, волнистые своды, резервуары, трубы и др).
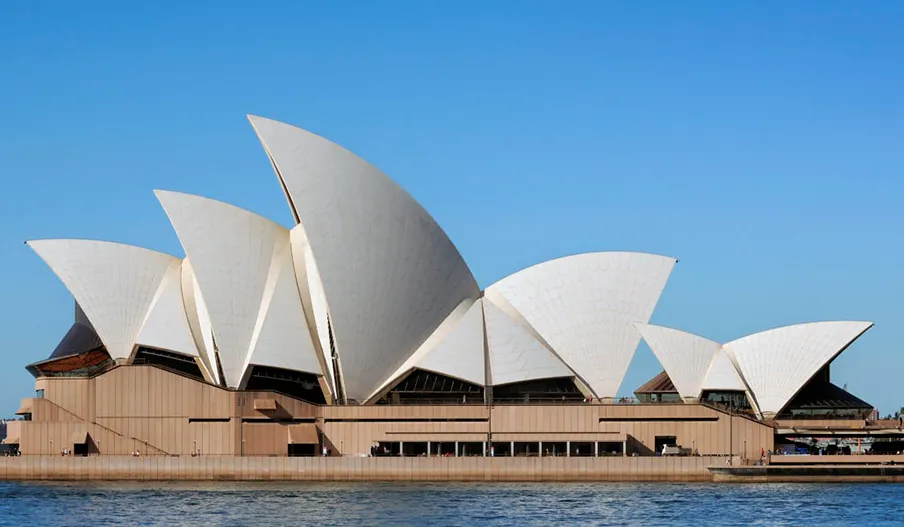
Одним из самых известных примеров ферроцементной конструкции является Сиднейский оперный театр. Открыть изображение в новом окне
ИСПОЛЬЗОВАНИЕ АРМОЦЕМЕНТА В РЕЗЕРВУАРАХ ДЛЯ ВОДЫ
В 2017 году на кафедре гражданского строительства в Landmark University (Нигерия) провели лабораторные и полевые исследования строительства резервуаров для сбора и хранения воды малой и средней ёмкости, и обнаружили, что армоцементные конструкции имеют преимущество перед другими альтернативами. Определяли лучший метод среди: (1) Кладка кирпич/камень; (2) Армированный бетон (R.C.C); (3) Листы стали/G.I.; (4) Армоцемент (ферроцемент); (5) Бамбуковый армированный бетон; (6) Пластик армированный волокном; (7) Композитная конструкция с использованием кирпича и ЖБК/ферроцемента; и (8) Потиэтилен высокой плотности.
Оказалось, что армоцемент идеально подходит для строительства резервуаров для хранения воды, благодаря его более высокой устойчивости к растрескиванию, ударам, перегрузкам и миграции влаги. Он получил более высокие баллы по безопасности, экономичности, простоте в строительстве и обслуживании даже в очень труднодоступных отдаленных районах.
«Конструкции, изготовленные из ферроцемента, тоньше, чем у железобетонных конструкций, легче по весу, следовательно, нуждаются в более лёгкой несущей конструкции. Строительство не требует тяжелой установки или оборудования или высококвалифицированного труда, необходимого для изготовления стали или железобетонной конструкции. Они не повреждаются при обычном ударе, чрезмерных нагрузках или пожаре, как в случае каменными и пластиковыми резервуарами. Они экономичны по сравнению с железобетонными, кирпичными, стальными и пластиковыми резервуарами. Благодаря своим преимуществам и легкой доступности составляющих его материалов, для большинства регионов армооцемент является идеальным строительным материалом для резервуаров для хранения воды в сельских и городских районах, как для крупных систем водоснабжения, так и небольших ирригационных систем. Резервуары могут быть установлены в подземных, частично подземных и частично надземных и надземных условиях».
Одним из первопроходцев в области исследований и разработок ферроцемента считается Исследовательский центр строительной инженерии в Газиабаде (Индия). Центр является одним из основных учреждений, работающих над системой сбора дождевой воды для Национальной технологической миссии. Центр проделал значительную работу по разработке ферроцементных конструкций и многих технологий для производства ферроцементных изделий, таких как резервуары для воды, резервуары для хранения, септики, кровельные элементы, стеновые панели, оросительные каналы, крышки люков, обработка для защиты от протечек кирпичной кладки и железобетонных конструкций, биогазовые метантенки, запорные плотины и др.
АРМОЦЕМЕНТНЫЕ ЯХТЫ
Применяют армоцемент и для изготовления корпусов мало- и среднетоннажных речных и морских судов, строят на воде дебаркадеры, брандвахты, мастерские, отели, кафе и рестораны, которые уже десятки лет эксплуатируются на реках России, Украины и др. Если вы погружаете сталь в океан, вам лучше обернуть её качественным бетоном, иначе расходы на содержание этой стали (покраску) будут уничтожать доход, получаемый от конструкции. Это касается кораблей и всех стальных конструкций в реках, морях и океанах!
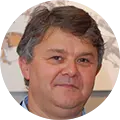
«Ферроцемент широко используется в судостроении в качестве дешевой замены стали, в жилых домах, трубах, резервуарах для воды и декоративных скульптурах» — объясняет Ремо Педрески, Профессор Эдинбургского колледжа искусств [ 5 ].
Немаловажным моментом является и то, что для строительства армоцементом расходуется минимальное количество материалов. Важна и распространённость сырья — армоцемент не нуждается для своего приготовления в крупном заполнителе, что существенно снижает его стоимость при массовом производстве.
В 1943 г. Нерви строит из армоцемента яхту «Неннел» длиной 12,5 м, а затем рыболовецкий катер большего размера. Яхта из бетона? — какой в этом смысл скажет читатель. Дело в том, что бичом традиционных судостроительных материалов (металл, древесина) является их низкая стойкость против действия коррозии и гниения, невысокая прочность, пожароопасность и трудоёмкость строительства.
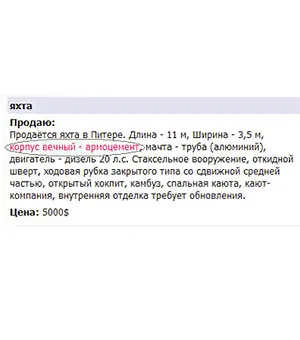
Например, братья Бирюковичи, создатели Киевского яхт-клуба, пионеры массового строительства яхт из армоцемента не только в СССР, но и всей Восточной Европе, утверждают, что за 6-8 лет эксплуатации деревянного судна суммарные затраты на его ежегодные весенние и осенние ремонты обычно превышают первоначальную стоимость нового корпуса, и даже при ежегодных ремонтах срок службы деревянных судов составляет всего 8-12 лет, а стальных — 18-25 лет. На своей армоцементной шхуне «Батьківщина» они ходили по Миссисипи, Большим Озерам и островам Карибского моря.
В 1960-х Мартин Йорнс (Martin Iorns) и Лу Уотсон (Lou Watson) из компании Fibersteel (Калифорния, США), запатентовали многослойный ферроцемент (laminated ferrocement) для строительства сверхпрочных и долговечных лодок. Процесс, который использовал Йорнс, имел 5 слоев и толщину корпуса 19 мм. Вместо раствора упакованного в арматуру, арматура в многослойном ферроцементе упакована в раствор. Сначала на форму корпуса напыляется тонкий (3 мм) слой раствора. Сверху укладывается просечно-вытяжная планка и слегка вдавливается.
Воздушные карманы и сухое уплотнение были устранены. Трудозатраты были значительно сокращены за счёт того, что не строили скелетный каркас и не связывали сетку вместе. Эта система прошла всесторонние испытания береговой охраны США в 1976 году при сертификации коммерческой мореходности, включая испытания на растяжение, сжатие, изгиб, сдвиг, удар и усталость. Многослойный ферроцемент был лучшим претендентом на доминирующую отраслевую разработку, но верфи перешли на использование стекловолокна и других материалов, чему способствовал более простой контроль качества, механизация производства, общественное мнение и страховые тарифы.
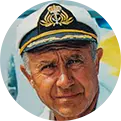
«Главный позитив армоцемента — его эксплуатационная надёжность. За десятки лет плаваний на армоцементных яхтах я неоднократно выходил из сложных ситуаций, в которых металлическое, деревянное или пластиковое судно наверняка погибло бы… В нашем яхт-клубе яхты из армоцементных скорлуп по нескольку сезонов не поднимаются из воды и чувствуют себя при этом отлично. Из армоцемента можно строить намного быстрее, чем из других материалов. Не нужны дорогие дерево, металл или пластик. К тому же квалификация строителей может быть не такой высокой. Ни один другой материал такой свободы не даёт» — объясняет Дмитрий Бирюкович, основатель Киевского городского крейсерского яхт-клуба (с 1967 г.).
Практика эксплуатации показывает, что наиболее дешевыми, долговечными и неприхотливыми являются именно железобетонные суда. Это объясняется, в частности, тем, что прочность цементных бетонов во влажных условиях эксплуатации (то есть именно в таких, в каких находится судно) со временем увеличивается. В этом отношении с цементом не могут конкурировать даже современные полимерные материалы. Уже одно только отсутствие необходимости в ежегодных ремонтах дает армоцементным судам хороший плюс технико-экономического их использования. При этом суда настолько прочны, что по окончании навигации армоцементные суда можно оставлять на зимовку во льду (если лёд не торосистый) и это не приводит к снижению их прочности.
Первое ж/б самоходное морское судно создал норвежский инженер Николай Фегнер в 1917 году (Namsenfijord). В годы II Мировой войны в США были построены 24 железобетонных судна и 80 барж. В мореходной Англии катера из армоцемента строят с 1962 г, они не уступают по прочности стальным (материал корпуса обладает упругостью, трещиностойкостью и коррозионной стойкостью), их стоимость на 40—60% дешевле и весят они на 5% легче деревянных.
До профессионального интереса Пьера Луиджи Нерви, давшего армоцементу путевку в жизнь, интерес к армоцементу в мире уже был, выше мы уже говорили о строительстве в 1849 году во Франции архитектором Ламбо лодки из армоцемента. Но интерес итальянского инженера был куда более сосредоточен — он знал, что пространственные тонкостенные конструкции требуют наименьшего расхода материалов, поскольку в них отношение собственной массы к полезной нагрузке минимально. При этом Нерви был архитектором и геометрия строительства его интересовала не в меньшей степени — тонкостенные конструкции позволяют использовать положительные свойства железобетона с наибольшей эффективностью благодаря приданию им рациональных геометрических форм.
В 1946 году его фирма строит экспериментальное здание — небольшой склад из листов армоцемента толщиной всего три сантиметра. В 1948-49 гг. Пьер Луиджи Нерви впервые в мире перекрывает тонкостенным сводом из армоцементных элементов зал выставочного павильона в г.Турине. В последующие годы, благодаря особо прочному армоцементу, он с легкостью перекрывает огромные пролеты сводами из сборных бетонных элементов (никогда ранее не применявшихся с таким размахом). Выходя за пределы гражданского строительства, Нерви выступил с предложением строительства из бетона, укреплённого стальными сетками, морских судов и даже авианосцев (созданы опытные образцы). Но широкое строительство судов из армоцемента в различных странах, включая и СССР, началось только с 1964 г. Дальнейшее творчество Пьера Луиджи Нерви связано с совершенствованием армоцементных «скорлуп», поиском разнообразных архитектурных форм и конструкций (1950—60-х гг).
АРМОЦЕМЕНТНЫЕ ЗДАНИЯ
Смелость и оригинальность конструктивных решений Нерви, основанных на точном инженерном расчёте, открытость и функциональная целесообразность пространственной организации сочетаются с яркой выразительностью структурных деталей (32-х этажное административное здание фирмы «Пирелли» в Милане, долгое время являвшееся самым высоким в Италии; Дворец спорта в Риме с пологим куполом на наклонно поставленных опорах, подобен гигантскому зонтику собранному из железобетонных ребер и панелей над залом в 5000 мест; плавательный бассейн Морской академии в Ливорно с его сводчатым покрытием; Дворец труда в Турине с оригинальными «зонтичными» перекрытиями, получивший первое место на конкурсе; здание ЮНЕСКО в Париже и др). Наиболее ярко выявлены технические, пространственные и художественные возможности тонкостенных конструкций из сборных армоцементных элементов талантливым итальянским инженером — в комплексе спортивных сооружений, осуществленных в Риме для Всемирной спортивной олимпиады 1960 года.
Ферроцемент начинает использовался в крупных общественных зданиях, а также в домах, только в 1950-х г. Например, в то время вокруг Санта-Барбары (Калифорния, США), существовало сообщество строителей, которые сочли, что низкая стоимость, а также сейсмостойкость и огнестойкость домов из ферроцемента идеально подходят для нужд региона.
Позже армоцементные конструкции начали применять с монолитными железобетонными элементами для строительства и в СССР — первая в Советском Союзе железобетонная конструкция сводчатой крыши над торговым рынком пролётом 15 м была построена в Ленинграде (1958). Благодаря использованию высокопрочного бетона и унифицированных элементов армоцементные конструкции значительно удешевились. При этом они позволяют создавать высокохудожественные элементы интерьеров без чужеродных украшений (отдельные элементы без особых затруднений образуют богатый декор).
Нерви — мастер конструкций, достигший большого совершенства в разнообразии форм, создаваемых путем сборки отдельных элементов. Своими работами он доказал, что армоцементные конструкции не только экономичны, но могут быть и художественно полноценными. Армоцемент обладает особой пластичностью и позволяет формировать конструкции абсолютно любых конфигураций. И его работы высоко оценены его соотечественниками. В 1947 году Нерви руководит кафедрой конструкций на архитектурном факультете университета в Риме, в 1950-1952 годах работает в Латинской Америке, где ведет курс архитектурных конструкций на архитектурном факультете университета в Буэнос-Айресе. Из-под его пера вышли такие научные труды, как «Строительство — искусство или наука?» (1945) и «Строить правильно» (1955). В 1960 году по рекомендации Королевского общества английских архитекторов Луиджи Нерви была присуждена золотая медаль за достижения в области архитектуры.
Постройки Нерви сыграли значительную роль в развитии конструктивных и архитектурных форм нашего времени. Они и сейчас продолжают оказывать влияние на архитекторов и конструкторов разных стран, потенциал заложенный в армоцементных конструкциях сегодня до конца не раскрыт.
В современной истории вклад в развитие тонкослойных цементных конструкций внесли вклад знаменитые инженеры, чьи работы всегда вызывают восторг: Antoni Gaudi (1900-е), Robert Maillart (1930-е), Pier Luigi Nervi (1940-е), Eduardo Torroja (1940-е), Felix Candela (1950-е), Euro Saarinen (1950-е), Heinz Isler — (1970-е), Eladio Dieste — (1980-е). Эти мастера точно измеряли и строили физические модели, не прибегая к сложным математическим вычислениям или компьютерам.
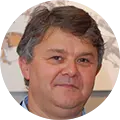
Феликс Кандела был испанским архитектором, инженером и строителем, работавшим в Мексике. Как и Нерви, он также был сторонником простоты формы и широко использовал гиперболические параболоиды. Эти формы с двойным изгибом были очень прочными, что позволяло использовать минимальный объем бетона. Один известный пример, ресторан Los Manatiales в Сочимилько, построенный в 1958 году, имеет пролет корпуса 45 м и толщину бетона всего 4 см [ 5 ].
Одно из лучших произведений Сааринена (Euro Saarinen) — проектировка Центра полетов TWA, терминала международного аэропорта имени Джона Ф. Кеннеди в Нью-Йорке (США). Является новаторским примером тонкостенной конструкции, состоящей из железобетонной оболочки поддерживаемой по углам. Чтобы спроектировать эту крышу, Сааринен сотрудничал с Чарльзом С. Уитни и Бойдом Г. Андерсоном из Ammann & Whitney. TWA представляет собой 2-х этажное здание. Тонкая бетонная оболочка крыши перекрывает пространство с минимальным количеством материала.
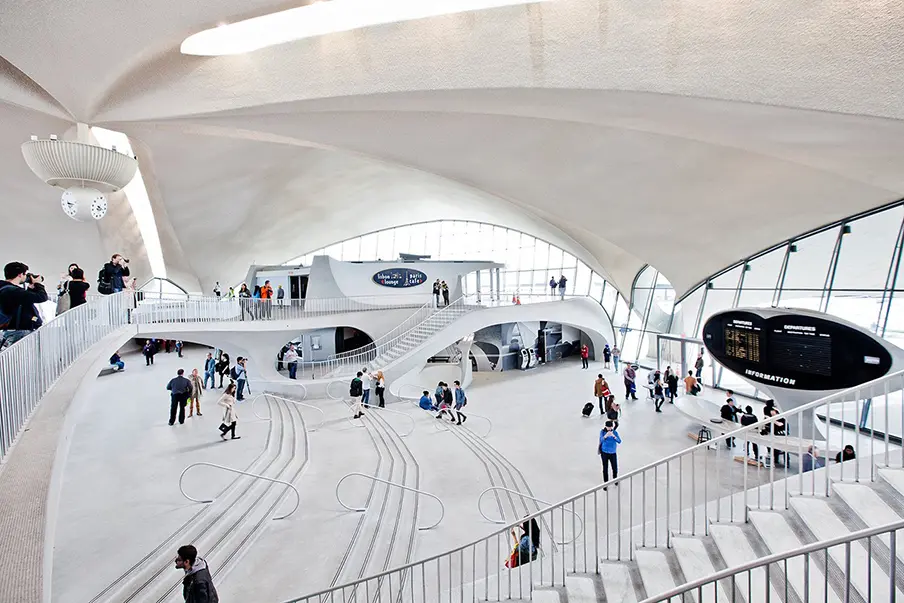
Центр полетов TWA, терминал международного аэропорта имени Джона Ф. Кеннеди (Нью-Йорк, США). Увеличенную фотографию открыть в новом окне
Сегодня в США строительство домов из классического ферроцемента большая редкость, технология перешла в панельную форму (SCIP). Одним из «могикан» является Стив Корнхер (Steve Kornher), который со своей компанией Flying Concrete строит в Центральной Мексике. Он предлагает 400-летнюю гарантию на крыши и предпочитает сводчатую конструкцию из-за прочности.
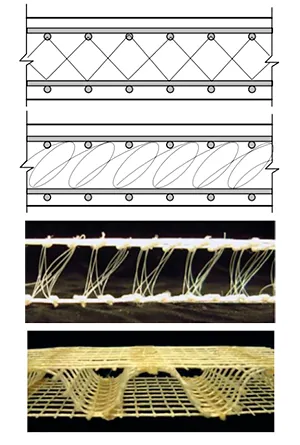
Развитие научного подхода к изучению и прогнозированию свойств армоцемента началось в конце 1960-х гг. на фоне интереса судостроителей-любителей, что было поддержано группой Национальной академии наук США в 1973 г. [ 6 ]. Это привело к формированию Комитета по ферроцементу Американского института бетона в 1975 г. и созданию Международного информационного центра по ферроцементу (IFIC) в Бангкоке, Таиланд (1976). В 1979 г. был сформирован научный комитет RILEM по ферроцементу.
В 1980-е годы прогресс ускорился благодаря фундаментальным исследованиям, публикациям, симпозиумам и кратким курсам. В 1984 году ферроцемент использовался при строительстве вибрационного стола для крупномасштабного моделирования землетрясений в государственном университете Нью-Йорка в Буффало (США).
В 1988 несколько методов строительства армоцементом описываются в Руководстве ACI [ 7 ]. В 1991 г. было основано Международное общество ферроцемента (IFS) с целью содействия развитию, распространения знаний и поощрения практического применения ферроцемента. Первый модельный кодекс ферроцемента опубликован в 2001 г., чем заложена основа для управляемого распространения, видения и разработок [ 8 ].
ИНДУСТРИАЛЬНОЕ СТРОИТЕЛЬСТВО ФЕРРОЦЕМЕНТНЫХ КОНСТРУКЦИЙ
Мы видим, что ферроцемент существует уже более 170 лет. Однако прогресс в области этих конструкций практически остановился на протяжении более 100 лет и набрал исключительную скорость только в течение последних четырех десятилетий. Этому способствовал прогресс строительных норм и правил в отношении ферроцемента (прежде всего в США), а также развитие компьютерного моделирования, появление программного обеспечения для цифрового проектирования, которое само по себе склонно к криволинейной геометрии армоцементных конструкций [ 9 ]
Используя мощь цифрового проектирования, исследователи из ETH Zurich построили прототип ультратонкой изогнутой бетонной крыши ферроцементной конструкции. Это скорее арт и выставка, чем массовая технология строительства. В отличии от SCIP.
Технология панельного строительства SCIP впитала в себя лучшее из армоцементной конструкции, и добавила индустриальности, которой ферроцементу всегда не хватало. Если строительство классических ферроцементных конструкций это всегда кастом, где нужно проволка за проволокой создать армирование для последующего нанесения бетона (site-assembled reinforcement cage), то в случае с SCIP у вас префабрикейтед, уже готовая к нанесению бетона панель.
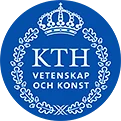
«Большие трудозатраты при строительстве традиционным ферроцементом можно снизить. Созданные компьютером проектные схемы позволяют производить в цеху готовый проволочный каркас, для использования на месте. Возможны многие усовершенствования, в том числе новые материалы, компьютерное моделирование и анализ» — объясняет доктор Ян Луговский, защитивший диссертацию на тему энергопассивных домов на основе ферроцемента в Королевском Технологическом Институте Швеции [ 4 ].
Ниже видео проекта Mesh Mold (Германия), который также стремится уйти от кастомизации. Являясь архитекторами и инженерами, они знают фантастические свойства железобетона, который способен выдерживать высокие растягивающие и сжимающие нагрузки, при относительно низкой стоимости и широкой доступности. Но особенно они любят его за возможность создавать свободу форм и эстетически потрясающий скульптурный дизайн. Однако «возведение таких криволинейных конструкций подразумевает очень большие затраты с точки зрения опалубки. Например, для двояковыпуклых поверхностей затраты могут достигать до 75% от стоимости конечной конструкции [ 10 ].
«Кроме того, такая опалубка обычно изготавливается в виде единственной в своем роде формы, которая используется только один раз и не подлежит вторичной переработке. Следовательно, современные технологии производства нестандартной архитектуры из железобетона вряд ли являются экономически или экологически устойчивыми, даже если возводимые конструкции обладают высокой эффективностью» — поясняют участники Mesh Mold, работающие над роботизированным процессом строительства ферроцементных конструкций. «Двухметровый строительный робот гибки и сварки проволок на гусеничном ходу In situ Fabricator специально устраняет эти ограничения, предлагая новый строительный процесс, основанный на цифровом производстве для производства сложных железобетонных конструкций. Проект стал финалистом Swiss Technology Awards. [ 11 ]
Видео от проекта Mesh Mold. Двухметровый строительный робот на гусеничном ходу In situ Fabricator играет центральную роль в процессе строительства ферроцементных конструкций.
Анизосетка
Бетон имеет слабость в сопротивлении растягивающим напряжениям, что проявляется в виде фрагментации, сколах и коробления поверхностей. Во время взрыва образовавшиеся фрагменты могут перемещаться с высокой скоростью что угрожает безопасности людей, находящихся внутри и вблизи конструкции. Чтобы улучшить характеристики ж/б конструкций нужно повысить прочность на растяжение и пластичность, а это возможно если использовать не периодическую арматуру, силовое действие которой аналогично стрингерным рёбрам, а стальную сварную сетку.
«Согласно существующим формулам пробития, конструкционные элементы, для защиты от баллистических ударов снарядов, имеют более высокие характеристики. Но с ростом прочности бетона, из-за его относительно высокой хрупкости, увеличиваются отколы на задней поверхности конструкции. Поэтому важно повысить ударную вязкость элементов ж/б конструкций. Одним из решений является армирование проволочной сеткой и волокнами» [ 12 ].
А если стальную сетку усилить вспомогательными ребрами жесткости, то получаем ортогональную сетку — жесткий и прочный объемно-пространственный каркас иерархической анизосетчатой усиленной панели (Hierarchical Anisogrid Stiffened Panels, HASP). «Анизосетчатые элементы конструкции обладают значительными преимуществами по сравнению с традиционными аналогами со стрингерными ребрами за счет исключительной прочности и жесткости однонаправленных композитных ребер, которые используются в качестве основных несущих элементов» [ 13 ].
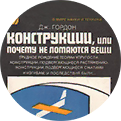
«Материалы, поведение которых напоминает поведение решетки, называются анизотропными (или иногда аллотропными), что по-гречески означает «различные в различных направлениях». Дерево, ткани и почти все биологические материалы анизотропны, причем каждый по-своему. Ткань для одежды является самым распространенным рукотворным материалом, и она в высшей степени анизотропна. Различия между материалом и конструкцией довольно туманны, и ткань, хотя портные и называют её материалом, на самом деле представляет собой конструкцию, состоящую из отдельных нитей, перекрещивающихся под прямым углом, и ведёт себя при действии нагрузкой почти так же, как и решетчатая стенка балки или фермы». [ 14 ]
Анизосетки (анизогрид, Anisogrid), изосеточные или анизорешетчатые конструкции — представляют собой решетчатые структуры (они же сетчатые оболочки), состоящие из повторяющегося симметричного рисунка пересекающихся окружных, винтовых и/или осевых ребер [ 15 ].
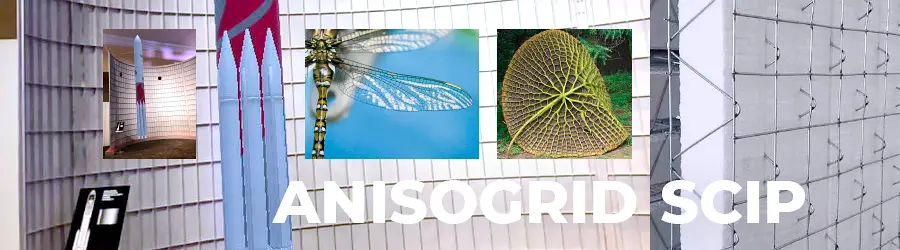
Изосеточные решения широко распространены в живой природе, как во флоре, так и в фауне. В наши дни анизосеточные решения считаются перспективными. Открыть изображение в новом окне
Благодаря превосходной весовой эффективности и стойкости к повреждениям, элементы конструкций из анизосеток нашли широкое применение в авиационной, морской и аэрокосмической промышленности. С целью создания конструкций критического веса анизосетчатые композитные оболочки применяются для космических ракет-носителей, в качестве промежуточных ступеней и конических переходников с 80-х годов как у нас, так и в NASA.
Сетчатые конструкции являются основными несущими платформами (цилиндрическая часть оболочки) отечественных космических аппаратов [ 16 ], их использование снижает вероятность повреждения аппарата и повышает его надежность. Композитные сетчатые конструкции имеют хорошие перспективы для использования в качестве несущих элементов планера самолета [ 17 ].
Они обладают значительными преимуществами перед традиционными аналогами со стрингерными ребрами за счёт исключительной прочности и жесткости однонаправленных композитных ребер, которые используются в качестве основных несущих элементов [ 18 ]. В частности, ребра жесткости могут увеличить жесткость на изгиб и сдержать общий изгиб панели: «сетчатые конструкции демонстрируют высокую устойчивость к продольному изгибу за счет способности перераспределять нагрузку по множеству направлений» [ 19 ].
Для аэрокосмического применения основной привлекательной причиной использования такой техники является создание высокопроизводительных и сверхлёгких конструкций. Сэндвич-панели аэрокосмического класса обычно производятся с использованием относительно дорогих материалов, таких как облицовочные панели из композитного графита/эпоксидной смолы и высокоэффективного алюминия или композитных материалов с сотовой сердцевиной. В последние несколько десятилетий сэндвич-панели начали применяться в и строительной отрасли. [ 27 ]
Геодезические конструкции (Geodetic structure) являются ещё одним вариантом сетчатых оболочек, их отличает сферическое (купольное) исполнение, которое даёт отличное сопротивление сдвиговым нагрузкам. Такая конструкция допускает локальное повреждение ребер без заметного снижения несущей способности.
Идея использования сетчатой структуры в конструкции самолетов возникла ещё во времена Второй мировой войны. В США Дж. Йетсом в 1941 году был сконструирован двухместный деревянный аэроплан «The Pixweve CT-6» с применением сетчатой структуры в конструкции крыльев, фюзеляжа и элементов управления [ 20 ]. Авиационные изделия с тонкостенной сетчатой оболочкой получались лёгкими и прочными, и при этом относительно низкой стоимостью. Их внедрение в авиастроительную отрасль снижало массу самолета (на 28% легче традиционной конструкции), увеличивало ресурс и себестоимость, а также ремонтопригодность в неподготовленных для обслуживания условиях. Реализация анизогридной концепции вляется перспективным направлением развития конструктивно-технологических процессов в авиационной технике. [ 21 ]
Многослойная стеновая конструкция
Никто не хочет зимой иметь промезшие стены и переплачивать за обогрев помещений. Постоянный рост нормативных требований к тепловой защите наружных стен зданий привёл к тому, что в вместо однослойных стен, которые уже не способны обеспечить требуемую тепловую ёмкость и сопротивление теплопередачи, получили широкое применение трёхслойные конструкции с эффективным утеплителем. Получается многослойная конструкция: несущий материал + утеплитель + защита утеплителя, которая создаёт тепловой комфорт в помещении и снижает затраты на его отопление. Также она менее склонна к перегреву летом, сохраняя внутри помещений комфортную температуру, что экономит энергию и ресурс кондиционерного оборудования.
Но многослойные стены совсем не новинка — на Руси строили массивными толстыми каменными, а также трехслойными стенами. Например, стены храма Рождества Богородицы, возведенного в XVII в. в Саввино-Сторожевском монастыре являются трехслойными: внутренняя и наружная части стен выполнены из плотного камня, а пространство между ними заполнено более легким известняком. Этот храм простоял несколько веков и до сих пор находится в хорошем состоянии без каких-либо серьезных разрушений.
Считается, что в новой истории идея многослойных строительных элементов впервые была использована в гражданском строительстве в 1849 году Виллианом Фэйрбэрном при испытаниях композитных балок с использованием дерева и бетона для создания конструкции мостов [ 22 ]. Но это не так.
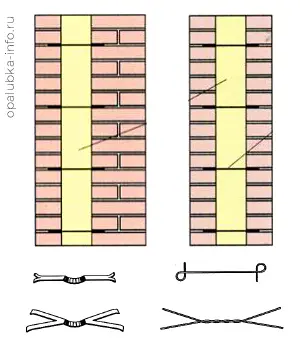
Первым, кто в новой истории начал возводить трёхслойные стеновые системы на строительной площадке, был русский инженер А.И. Герард. В 1829 году в кладке между кирпичами он расположил засыпной органический утеплитель (опилки, торф, мох), напомним, что к этому времени кирпич уже активно использовался — первые кирпичные строения появились в Москве в 1450 г.
Слои соединялись металлическими скобами, закрепляемыми в просверленные в кирпичах отверстия. Также им были разработаны конструкции стен из 3-х кирпичных стенок разделенных воздушными прослойками. В 1930-е годы появились технические решения облегченных стен высотой до 5 этажей. Связь между слоями выполнялась гибкими стальными соединителями либо перевязкой кирпичом. [ 23 ]
В начале нулевых жители сталинки напротив Центрального телеграфа на ул. Тверской (Москва), при ремонте ванной часть старой кладки развалилась, стену пришлось разобрать. Внутри обнаружили… камыш, который использовался в качестве утеплителя.
В массовом строительстве 3-х слойные конструкции наружных ограждений стали активно применяться с 1970-х гг. В качестве теплоизолятора использовались цементный фибролит, минеральная вата и пенополистирол. Толщина слоя утеплителя составляла 50 мм.
Сборный железобетон
Ограждающим конструкциям из сборного железобетона (Precast Concrete) скоро исполнится 120 лет, изначально панель состояла из одного слоя бетона и устанавливалась в зданиях для облицовки.
Один из самых ранних образцов стен из ж/б панелей был построен в 1906 году [ 24 ]. Эта сборная стена (tilt-up wall) была создана путем заливки 2-дюймового слоя бетона (51 мм), покрытого 2-дюймовым слоем песка (51 мм), а затем заливки второго 2-дюймового слоя бетона (51 мм). Фактически это была сэндвич-панель, но ещё без утеплителя. Бетонные панели соединялись стальными стяжками, конструкция которых неизвестна. При укладке песок промывали пожарным шлангом.
В результате Первой мировой войны из-за глобальной нехватки материалов и рабочей силы, которую она принесла с собой, что привело к увеличению затрат на строительство, стремительно развивается индустриальное строительство из сборного железобетона. Начиная с 1918 года строители начинают задаваться вопросом, зачем строить дважды, один раз из дерева (опалубка) и, наконец, из бетона (монолит). Англия, Западная Европа, Европа и Россия, наиболее сильно пострадавшие от войны, с 1918 по 1939 год проводят исследования и реализуют производство стандартных сборных деталей, достигая большой прогресс в сборке блоков как для индивидуальных домов, так и для многоэтажных домов.
Так городской архитектор и планировщик Франкфурта Эрнст Мэй (Ernst May), который учился у Анвина, уделял много внимания естественному гелиоморфному планированию города, и пытался разработать новые методы строительства и жилищного производства. Он экспериментировал в 1920-х годах с сборными системами во Франкфурте — сборные железобетонные панели производились на месте, а затем собирались кранами.
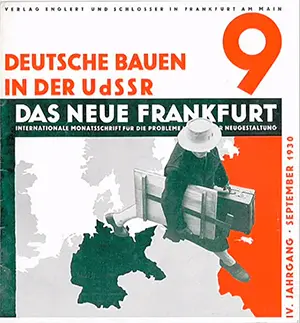
ИНДУСТРИАЛЬНОЕ СТРОИТЕЛЬСТВО
В 1930 году Мэя пригласили в Советский Союз, куда он привез свои идеи и майскую бригаду, как их называли. Советское правительство поставило задачу спроектировать новый социалистический город Магнитогорск, который был центром сталелитейной промышленного производства на Урале, а заодно и начать или хотя бы предложить, как рационализировать советскую стройиндустрию для освоения серийного массового жилья. В 1930 году он разработал генеральный план Магнитогорска.
После второй мировой войны, которая вызвала нехватку жилья, специализированной рабочей силы и материалов, сборный железобетон стал настоящим прорывом, поскольку выводил строительную отрасль на новый уровень — он не требователен к материалам и высококвалифицированной рабочей силе, имеет более короткие сроки выполнения и более низкие затраты.
Первые попытки массового возведения монолитных железобетонных зданий (бетонирование выполняется непосредственно на строительной площадке) в России предпринимались еще в 1930-е годы, во времена расцвета конструктивизма, он начался ещё в 1920-е годы — застроенный фахверковыми домами рабочий поселок в Иваново, был одним из первых образцов массового промышленного строительства в СССР. В те годы жильё для рабочих, обычно представляло собой временный барак или общежитие поквартирного поселения, многие из них не имели удобств.
В мае 1930 года ЦК ВКП(б) принял постановление «О работе по переустройству быта», где подчёркивалась важность формирования нового социалистического образа жизни и вскрывались допущенные ранее ошибки в жилищном вопросе. В густозастроенных районах городов строились трех-пятиэтажные секционные дома, создавались новые кварталы, жилые комплексы, строились новые промышленные города. Вся страна превратилась в строительную площадку, поскольку массовое крупноблочное каменное жилищное строительство получило такую же важность, как и развитие промышленности. Это привело к тому, что уже в период своего становления советская архитектура активно влияла на развитие современного жилища в других странах.
Новые типы жилищ, новые объемно-пространственные решения дома, варианты совмещения жилых и коммунальных помещений, пространственные типы жилых единиц, рациональная планировка и оборудование квартиры, новые типы односемейных, блочных, секционных и односекционных были разработаны жилые дома, крупногабаритное и мобильное жилье и т. д.
СССР стал первой страной в мире, где для решения жилищной проблемы была сделана ставка на индустриальное крупнопанельное ж/б строительство. Первые заводы по производству сборного железобетона в СССР появились буквально перед самой войной в 1941 г., но широкому и всестороннему применению сборного железобетона ещё 15 лет будет препятствовать низкий уровень механизации строительства, отсутствие мощных монтажных кранов и оборудования для производства железобетонных изделий.
Применение сборных конструкций для строительства объектов энергетики началось в 1952 г. с сооружения теплоэлектростанций Василевической (Белорусия), Прибалтийской (Эстония) и Симферопольской. На Конаковской ГРЭС сборность достигла 85%, в наземной части Змеевской ГРЭС — 97%. Перевод энергетического строительства на индустриальные способы позволял резко повысить темпы ввода тепловых электростанций. В 1961 г. было, например, введено более 60 ГРЭС общей мощностью свыше 31 млн. кВт.
Прорыв в организации массового выпуска сборных ЖБИ произойдёт с Постановлением ЦК КПСС и Совета Министров СССР от 19.08.1954 г. «О развитии производства сборных железобетонных конструкций и деталей для строительства». В результате была создана самая крупная в мире индустриальная промышленность сборного железобетона — если в 1954 г. было выпущено около 2 млн м³ сборных железобетонных изделий, то в 1970 г. общий выпуск сборного железобетона составил около 84 млн м³. С 1955 по 1985 год объем производства сборного железобетона вырос с 6,2 миллиона м³ до 151 миллиона м³ в год. Индустриализация позволила поднять производительность труда на 300% в целом по стране, а унификация изделий и переход на заводской выпуск сократила стоимость строительной продукции почти на 60%.
В послевоенные годы потребность в 250 тыс. домов в год, привела Францию к первым тендерам на поставку систем, таким как Quaide Rotterdam в Страсбурге на 800 домов. Промышленно развитую систему серийного производства на заводах в Европе предложила FabricaMontesson, которая в 1952 г. получила контракт на поставку 4 тыс. сборных панельных домов, 2 000 домов в год. [ 25 ]
ПРЕИМУЩЕСТВО СБОРНОГО ЖЕЛЕЗОБЕТОНА
Сегодня в США, наружные стены многоэтажных зданий почти везде выполняются сборными, поскольку бетонирование таких элементов на месте оказывается существенно более трудоёмким. Действительно, серийное строительство сборными железобетонными элементами имеет множество преимуществ:
- в разработке: позволяет основную часть работ по возведению зданий перенести со строительной площадки на завод с высокоорганизованным технологическим процессом производства изделий, что, в конечном итоге, дает определенный технико-экономический эффект: стабильное качество продукции через организацию пооперационного контроля; стандартизация различных строительных подсистем (конструкций, ограждений, перегородок), точность размеров и строительства (составы бетонов и конструкции опалубочных форм позволяют получать высокоточные изделия с допусками в десятые доли миллиметра), возможность в ряде конструкций в 2—4 раза сократить расход стали, ускорение строительства и высокая производительность на месте, готовность конструкции. В заводских условиях возможно изготовление конструкций по двух-трехстадийной технологии с применением в качестве декоративных элементов различной текстуры и фактуры поверхностей, цветовой гаммы, включая отделки из естественного камня или керамики.
- в организации и планировании: финансовое планирование, координация деятельности, эффективность управления строительством на площадке.
- расходы: отмена простоев, использование неквалифицированной рабочей силы, более точные бюджеты, контроль материалов, 100% оптимизация и эффективное использование ресурсов.
МИНУСЫ СБОРНОГО ЖЕЛЕЗОБЕТОНА
Однако, наряду с достоинствами, классическое сборное ж/б панельное строительство имеет и недостатки — панели имеют значительный вес, что приводит к более высокой стоимости фундамента и строительства в целом, их использование особенно нежелательным на тех строительных площадках, которые страдают от низкой несущей способности или имеют пучинистые почвы. Есть вопросы по высокой себестоимости изделий на заводах сборного железобетона, значительных транспортных расходах — всё это снижает общую технико-экономическую эффективность строительства.
Отдельно стоит отметить плохую герметизацию, которая буквально вымывала тепло из здания: щели между стеновыми панелями, щели между плитами перекрытий. Более массовое использование монолитного строительства при котором нет швов, позволило улучшить теплоизоляционные свойства здания.
Однослойные керамзито-бетонные панели имели термическую неоднородность из-за стыковых соединений, которую ухудшал человеческий фактор — качество уплотнения и утепления стыковых соединений в условиях советской стройки было низким — стыки протекали и промерзали, стены становились сырыми. Усугубляло проблему повсеместное несоблюдение технологии изготовления керамзито-бетона, они теряли теплоизоляцию из-за повышенной плотности панелей.
В зданиях с трехслойными панелями их ребра жесткости давали мостики холода, не нешены проблемы стыковых соединений. Проблемы были и с архитектурой — внешний вид бетонных стен был крайне непритязателен, цветных бетонов у нас не было, а краски были не надежны. Понимая эти проблемы, архитекторы пытались придать разнообразие зданиям за счет нанесения плитки на наружную поверхность стен.
Сегодня в России тысячи предприятий стройиндустрии, производящих ЖБИ, и большинство из них построены по технологиям 60-х гг ХХ века.
ЖЕЛЕЗОБЕТОН СЕГОДНЯ
Сегодня существует в основном три типа сборных железобетонных конструкций:
- каркасная конструкция (frame structure),
- конструкция жесткой стены (shear wall structure),
- каркасно-стеновая конструкция (frame-shear wall structure).
Сборные железобетонные сэндвич-панели (Precast Concrete Sandwich Panels, PCSP) широко используются в качестве наружного защитного (ограждающего) элемента в стеновых конструкциях жесткости (exterior protective component in shear wall structures) и каркасно-стеновых конструкциях (frame-shear wall structure) благодаря более высокой термостойкости по сравнению с обычной железобетонной стеновой панели (Reinforced Concrete, RC). PCSP в основном состоит из двух внешних RC слоев, изоляционного слоя в форме сердечника и соединителей, которые соединяют эти три слоя вместе.
КАРКАСНОЕ НА ОСНОВЕ СБОРНОГО ЖЕЛЕЗОБЕТОНА
Каркасное строительство на основе сборного железобетона сегодня выходит в лидеры: по данным «Инком-Недвижимость», с 2016 по 2021 год предложение квартир в панельных новостройках Москвы снизилось с 15% до 4%, остальной объем занимают лоты в монолитных домах и немногочисленные кирпичные.
Нагрузка в многоэтажном монолитном здании передается на несущий каркас, который отливается из бетона, поэтому отпадает необходимость в толстых внутренних перегородках. Конструктивная жесткость монолита дает равномерную осадку всего дома, что позволяет делать ремонт в квартире сразу после введения дома в эксплуатациюв то время как в панельном доме производить качественную отделку не советуют раньше чем через год после окончания строительства — при усадке фундамента в нецелостной конструкции существует большая вероятность появления трещин.
Квартиры в таком здании идеально приспособлены для индивидуальных перепланировок, поксольку тяжелые конструкции опираются на монолитные колонны, а не на стены, как в панельных домах, поэтому внутренние стены можно переместить или убрать без риска нарушить прочность несущих конструкций. Обладая плюсами монолитной технологии, каркасная технология на 25-30% дешевле крупнопанельного, здесь нет ненадежных арматурных стыков и промерзающих швов как у крупнопанельных (PCSP) домов. Минус один — значительные первоначальные капитальные вложения от 2,5-3 млн долларов.
Теперь вы знаете почему в высотном строительстве часто используют панели SCIP в качестве герметизации готового каркаса.
Сэндвич панель
Под термином «сэндвич-панель» понимается строительная многослойная конструкция, имеющая бескаркасный тип. Сделаем небольшой экскурс в историю появления сэндвич-панелей.
Сэндвич-конструкция давно и широко используется в различных отраслях промышленности, как в конструкционных, так и не в конструкционных целях, например в упаковке (гофрированный картон и др.), защитных материалах и др. [ 26 ] Такие конструкции аэрокосмическая промышленность использует с 1950-х годов. Для аэрокосмического применения основной привлекательной причиной использования такой техники является создание высокопроизводительных и сверхлёгких конструкций. Сэндвич-панели аэрокосмического класса обычно производятся с использованием относительно дорогих материалов, таких как облицовочные панели из композитного графита/эпоксидной смолы и высокоэффективного алюминия или композитных материалов с сотовой сердцевиной. В последние несколько десятилетий сэндвич-панели начали применяться в и строительной отрасли. [ 27 ]
Пластины, панели и оболочки широко используются и природой, и техникой, но, чем они протяженнее и тоньше, тем меньше их жесткость на изгиб и критические нагрузки потери устойчивости. В принципе всё, что увеличивает жесткость стержня или пластины на изгиб, увеличивает и ее сопротивление выпучиванию при продольном сжатии. Один из методов повышения устойчивости состоит в установке панели или стержня с помощью тросов и растяжек (метод, никогда не используемый в растениях). Другой и, возможно, более предпочтительный метод состоит в устройстве рёбер жесткости, гофрировании для использовании ячеистых конструкций.
В инженерных конструкциях жесткость панелей и оболочек увеличивается с помощью стрингеров и шпангоутов, которые приклеиваются, приклепываются или привариваются к обшивке, хотя это и не всегда самый простой или самый дешевый путь. Другой путь решения проблемы состоит в изготовлении оболочки из двух разнесенных слоёв, пространство между которыми содержит возможно более лёгкий наполнитель. Конструкции такого типа называют «сэндвич».
Сэндвич-панели впервые были использованы Э. Бишопом, гл. конструктором фирмы Хэвиленд. В 1930 г. он применил их в фюзеляже самолета «Комета», в качестве наполнителя использовалась лёгкая бальсовая древесина, а внешние слои сэндвича делались из прочной и тяжелой березовой фанеры, которая приклеивалась к наполнителю. [ 14 ]
Поскольку в качестве заполнителя были нужны более водостойкие и лёгкие материалы, сперва пришли ко вспениванию искусственных смол, а затем и к синтетическим (пенополистирол и др.). Конструкции типа сэндвича и наполнители с незапамятных времен используются в природе. Примером тому служат так называемые «плоские» кости нашего черепа, подвергающиеся действию изгибающих и сжимающих нагрузок.
Сэндвич-панели с 2-мя асбестовыми слоями и сердечником из ДВП уже широко использовались во времена Первой мировой войны. Появление различных типов клеев в США и Англии в 1930-х годах привело к появлению клееных сэндвич-панелей, их массово применяли в легких самолетах уже во Вторую мировую.
В качестве оболочек стен их впервые начали использовать в 1930-х годах при строительстве недорого жилья в Великобритании. Для стен своих недорогих домов Usonian (1930), знаменитый американский проектировщик Френк Л. Райт использовал 3 слоя фанеры склеенных двумя слоями смолы. Технологию назвали конструкционная теплоизоляционная панель, то есть СИП (Structural Insulated Panel, SIP).
Впрочем, исследования и испытания SIP-технологии проводились и в США, например, лабораторией лесных продуктов (FPL) в Мэдисоне, штат Висконсин. Лесная служба США (U.S. Forest Service) была обеспокоена темпами обезлесенья, и идея использования опилок вместе с химическим клеем им показалась интересной. Пыталась сохранить лесные ресурсы, в 1937 году они построили небольшой дом с оболочками SIP и сумели привлечь к нему достаточно внимания, чтобы его посвятила первая леди Элеонора Рузвельт. Они решили что панель может выдержать нагрузки чтобы полностью исключить традиционный каркас здания и вывела на рынок свой специально разработанный SIP, где он продавался в течение следующих 30 лет.
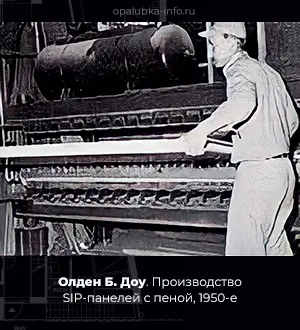
В 1947 году SIP изготавливали из фанеры и сердечника из спрессованного картона. До 1960 года технология SIP почти не имела сбыта в Англии, где жильё в основном возводилось сборными железобетонными сэндвич-панелями. [ 28 ].
Фанера и картон не давали достаточной теплоизоляции, поэтому впоследствии ученик Райта Олден Б. Доу, между торцами фанеры включил сердечник из пенополистирола (EPS). Олден Б. Доу, брат основателя Dow Chemical Company (кап. $70 млрд, в России с 2003), создал первую SIP-панель с сердечником из вспененного материала в 1952 г.
В конце 1960-х годов SIP в основном использовались в строительстве объектов специального назначения, таких как холодильные склады, использовались в авто- и судостроительной промышленности. Сообщалось, что жёсткие пенополистиролы использовались в качестве основного материала, в то время как бетон, фанера и металлические листы использовались для формования панелей SIP. Сегодня SIP подпадают под категорию интеллектуальных промышленных систем зданий (IBS), в 1970-х и начале 1980-х годов они получили резкий рост. [ 29 ]
Сэндвич-панели — просто удобный стройматериал. Что касается бетонной сэндвич-стены, то изначально конструкция состояла из двух железобетонных элементов, разделенных внутренним пространством. Соединители представляли собой закладные стальные соединители. Рост требований к энергоэффективности зданий и достижения лучших тепловых характеристик, привёл к использованию теплоизоляционных материалов, который установили в пустоты. Стальные соединители теперь имеют другую форму, чтобы избежать образования мостиков холода и проблем с влажностью.
Пенополистирол
Основное химическое соединение пенополистирола стирол, впервые было получено в 1831 году путём нагревания смолы бальзамного дерева Стиракс. Смола этого дерева использовалась в качестве душистого вещества в парфюмерии, антисептика и одного из компонентов состава для мумифицирования в Древнем Египте около 3000 лет назад [ 30 ]. В 1929 г. ученые компании DOW синтезировали стирол, из которого получен полимер — полистирол. Коммерческое производство полистирола было начато в 1930 г. компанией IG Farbenindustrie в Германии; его производство в США организовала Dow Chemical Company (1938).
Идея получения вспененного полистирола принадлежит шведским изобретателям, которые получили патент на изобретение в 1931 г. Благодаря изоляционным характеристикам, лёгкости, прочности и невысокой стоимости, сегодня EPS занимает одну из ведущих позиций в гражданском строительстве.
Что EPS отлично подходит для гражданского строительства, впервые обнаружили в Норвегии в 1960 г. — EPS отлично предотвращает промерзание грунта (что устраняет последующие проблемы с оттаиванием), и у него низкое поглощение влаги. Сегодня это популярный в России материал для утепления домов, во многих странах его используют в плитах перекрытия. В СССР сырье для производства пенополистирола — вспенивающийся полистирол был впервые произведен на Украине в 1965 г. Подробно о пенополистироле мы говорим тут.
Ж/б сэндвич-панель с утеплителем
Стеновая сэндвич-панель из сборного железобетона «бетон-утеплитель-бетон» впервые появилась в 1950-х г.
США. В Нью-Йорке (штат Нью-Йорк) в 1951 году для строительства целлюлозного завода построили производственные линии для изготовления сборных теновых панелей с утеплителем, которые имели длину 61 метр. Каждая панель была высотой 1,82 м и шириной 3,05 м. Панели имели общую толщину 14 см. «Панели представляли собой 51 мм слой изоляции из пеностекла и две армированные проволочной сеткой плиты из бетона плотностью 3000 фунтов на кв. дюйм, связанные вместе канальными полосами из просечно-вытяжного металла. Эти связи также служат усилением сдвига» [ 31 ].
СССР. В 1954—1955 гг. трестом Криворожстрой для наружных стен промышленного, корпуса были применены трехслойные железобетонные панели размером 6,0x1,5 м. Основой панели служила коробчатая железобетонная плита с высотой ребра 250 мм, а в качестве утеплителя был применен крупнопористый бетон на термозитовом щебне слоем толщиной 200 мм; поверх термозитобетона укладывался армированный фактурный слой толщиной 20 мм. Панель армировалась сварными каркасами и сетками из 6-мм катанки с ячейками 20х20 см. Термозитовый щебень имел объемный вес (в плотном теле) около 550 кг/м³; объемный вес крупнопористого термозитобетона 670 кг/м³; на 1 м³ термозитобетона расходовалось 160—170 кг цемента марки 400; вес-панели 3 т.
Трехслойные панели сплошного сечения из тяжелого бетона с термовкладышами из блоков безавтоклавного ячеистого бетона, предназначенные для стен производственных зданий с относительной влажностью воздуха до 60%, широко применялись при строительстве горнообогатительных комбинатов Криворожского бассейна.
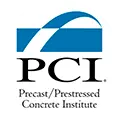
Институт сборного/предварительно напряженного бетона (США, 1997): «Интерес к этим панелям распространен во всем мире из-за их характеристик (передача нагрузки и изоляция здания), эстетики (можно создать любую архитектурную форму), адаптации (например, панели можно крепить к любому типу несущего каркаса), долговечности (сэндвич-панели), устойчивости к ударам, кражам и вандализму, а так же скорости монтажа и стоимости». [ 32 ]
Использование пенополистирола в качестве изолятора началось чуть позже, но уже к середине 1990-х большинство сборных сэндвич-панелей состояли из железобетона, пенополистирола и стальных соединителей. Во многом это заслуга принятых XXVI съездом КПСС «Основных направлениях экономического и социального развития СССР на 1981—1985 годы и на период до 1990 г», где предусмотрен ускоренный рост (в 1,7 раза) выпуска синтетических смол и пластмасс и преимущественное развитие производства и применения новых прогрессивных материалов и изделий, обеспечивающих снижение стоимости и трудоемкости строительства, экономию металла, уменьшение массы зданий и сооружений, повышение их теплозащиты.
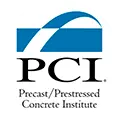
Институт сборного/предварительно напряженного бетона (США, 2011): «Сэндвич-панели обладают всеми желаемыми характеристиками обычных сборных железобетонных стеновых панелей, такими как долговечность; экономика; огнестойкость; большие вертикальные промежутки между опорами; и использовать в качестве несущих стен, несущих стен и подпорных стен. Кроме того, изоляция обеспечивает превосходные энергетические характеристики и защиту от влаги по сравнению со многими другими стеновыми системами. Твердая поверхность внутри и снаружи сэндвич-панели обеспечивает устойчивость к повреждениям вилочным погрузчиком, кражам и вандализму, а готовое изделие при желании не требует дополнительной обработки». [ 33 ]
Сегодня, в связи с огромным вниманием к стоимости энергии и изменениях в сертификации зданий в области энергетического и экологического проектирования (LEED, BREEAM и др.) снова возрастает спрос на эти термически и экономически эффективные конструктивные элементы.
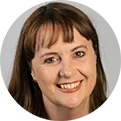
По словам генерального директора Национальной ассоциации сборного железобетона Австралии (NPCAA) Сары Бачманн, «сэндвич-панели из сборного железобетона и утеплителя, обладают множеством преимуществ, включая непревзойденную долговечность, огнестойкость и короткие сроки строительства. А благодаря своим превосходным тепловым характеристикам, они значительно снижают потребление энергии».
Как сегодня это выглядит на практике, можно подсмотреть у безусловного лидера по вводу жилья в 2021 году ГК ПИК, тут как работает оборудование для производства 3-х слойной железобетонной панели с эффективным утеплителем, а ниже их 45 минутный ролик об индустриальном строительстве, выпущенный совместно с каналом Discovery.
Скептики монолитного строительства указывают на крайне низкий коэффициент теплосопротивления бетона, отсутствие у него теплоизоляционных свойств. Да, камень тянет тепло — для непрогретого или неутеплённого дома это недостаток. Но в нормальных условиях, когда дом утеплён, этот «недостаток» его огромное достоинство! Потому что только с таким теплоёмким материалом как бетон и можно сделать так, что бы дом сам, с минимумом нагревательных и при полном отсутствии охлаждающих систем обеспечивал тепловой комфорт, сам собой, без вмешательства электроники, естественным путём, благодаря законам Природы. Теплоинерционность бетона нуждается в утеплении, собственно как и любой другой конструкционный материал — одновременно обладающего высокими конструкционными и теплоизоляционными характеристиками материала не существует.
В этом коротком выступлении Николаев Станислав Васильевич, научный руководитель ЦНИИЭП Жилище, сказал несколько важных вещей об индустриальном строительстве, экономичности панельного строительства, важности малоэтажного строительства и увеличения м² на 1 человека.
Монолитное многослойное домостроение рассматривается сегодня как один из перспективных видов создания малоэтажного жилфонда. Герметичные теплонакопительные ограждающие конструкции с эффективной наружной теплоизоляцией играют ключевую роль в правильной «домашней энергетике».
Несъемная опалубка
И хотя ценность бетона была давно признана, его широкому применению долгие десятилетия препятствовали высокие затраты на строительство из-за материалов для изготовления опалубочных форм, которые употреблялись и впоследствии выбрасывались. Недёшево обходилась и рабочая сила — для строительства ж/б стен требовалась сборка-разборка опалубки, что отнимает время и усложняет строительный процесс. Также имели место проблемы с креплением облицовки и установкой инженерных коммуникаций, а также вопросы интеграции изоляции с бетонной стеной.
Определённо существовал запрос на решение этих проблем, как и значительный интерес к разработке строительных материалов, которые включали бы несущий элемент и изоляцию в одном и том же продукте (2 в 1). И такой продукт появился — изобретение несъемной опалубки стало одним из полезнейших изобретений строительной отрасли второй половины XX века.
История несъемной опалубки началась с фибролита, который получил большое распространение во время Первой мировой войны. Немецкие войска использовали фебролит при строительстве временных зданий и это мало отличалось от обычного ж/б строительства — после застывания бетона опалубка из фибролита оставалась на месте и превращалась теплоизолятор.
Со временем несъемная опалубка принимала разные формы: в 30-х годах прошлого столетия была разработана и запатентована технология Durisol (Нидерланды); в Австрии получает развитие несъемная опалубка из щепоцементных плит Velox; в Швейцарии — цементные плиты с минерализованной деревянной стружкой.
История применения пенополистирола в качестве несъемной опалубки начинается не с его изобретения (Германия, 1930), а с разработки в Западной Германии (в начале 50-х гг.) технологии получения пенополистирола методом горячего формирования (в США этот метод пришел в 1954 г.). С тех пор лёгкие формы из пенополистирола придают требуемую форму монолитным бетонным или железобетонным конструкциям, возводимым на строительной площадке, и одновременно, благодаря высоким изоляционным характеристикам, служат их теплоизолятором. Впоследствии, в ж/б строительстве несъемная опалубка из пенополистирола стала применяться не только как форма для заливки бетона, но и как основа для его напыления методом торкретирования.
Использование в строительстве современных опалубочных систем значительно повышает технологичность процесса, сокращает стоимость и сроки возведения здания. Выше мы показали, что в историческом развитии индустриальное строительство движется от мелкоштучного строительства (камни, кирпичи) к блочному; от блочного к панельному; а от панельного к крупнопанельному. Это неудивительно, поскольку в серийном потоковом строительстве только так можно получить наиболее высокие технико-экономические характеристики строительного процесса.
Вот и подошли к рождению железобетонной сэндвич-панели с утеплителем несъемной опалубки SCIP, её история началась в 1964 году, кто первый сложил её в конструкцию, как развивается технология в новейшей истории тут.
#
Если вам было интересно прочитать — воспользуйтесь кнопкой Поделиться, лайк и коммент по ссылкам ниже, спасибо! Если у вас остались вопросы, вы можете спросить нас личным сообщением в Телеграм, написать электропочтой или в форму обратной связи (в нижней части страницы). Также вы можете задать вопрос публично в ЧАТ Телеграм или YouTube.
Используемые источники
[ 1 ] The Pioneers of Concrete Construction. 2004.
[ 2 ] Отчет по ферроцементу Комитета 549 Американского Института Бетона (ACI) ACI549R-18, 2018 г. ISBN: 978-1-945487-95-8
[ 3 ] Баладжи Балшанкар, С.С. Бендсур «Современные технологии строительства из ферроцемента в устойчивом строительстве». Журнал достижений в области науки и технологий [JAST]. Том: 19 / Выпуск: 2. Индия. DOI: 10.29070/JAST Апрель, 2022. Ссылка
[ 4 ] Ян Луговски «Проектирование и строительство ферроцементной коробки дома с суперизоляцией» Магистерский проект в области энергетических технологий. EGI-2013-046MSC Стокгольм, Швеция, 2013 г.
[ 5 ] Р. Педрески, «Форма, сила и структура: краткая история». Архитектурный дизайн Том. 78, № 2, стр. 12-19, 2008.
[ 6 ] Нааман, А.Е. «Механизмы усиления в ферроцементе» Диссертация, Департамент гражданского строительства, Массачусетский технологический институт. 152 стр. 1970 г.
[ 7 ] Комитет ACI 549, Руководство по проектированию, строительству и ремонту ферроцементом, ACI 549.1R-88, Строительный журнал ACI, Май-Июнь 1988 г., стр. 325-351. Также восстановлен как 549.1R-93 и опубликован в Руководстве ACI по Практике бетона, Американский институт бетона, Фармингтон-Хиллз, Мичиган, 27 стр.
[ 8 ] Ferrocement Model Code, Комитет IFS 10-01 (2001 г.) Международное общество ферроцемента, Азиатский технологический институт, Бангкок, Таиланд, 95 стр.
[ 9 ] Т. Валлиссер «Цифровой дизайн и Фабричные Методы» Руководство по современному бетонному строительству: Строительные методы, Характеристики Материалов, Экологическая Устойчивость. Под редакцией. М. Пик, Мюнхен: Институт международной Архитектуры и документации. Стр. 106–116. 2014
[ 10 ] Шиппер Х.Р., С. Грюнвальд «Эффективное использование материала благодаря умному методу гибкой опалубки» in Proc. ECO-Crete: Int. Symp. on Environmentally Friendly Concrete, Reykjavik, Iceland, 13-15 Aug. 2014
[ 11 ] Норман Хак и ещё 13 авторов «Mesh Mould: an on site, robotically fabricated, functional formwork» Март, 2017. Ссылка
[ 12 ] А.Н. Данцигер Д.З. Янкелевский «Реакция высокопрочного бетона на сильный удар снаряда» Международный журнал ударной техники, Том 18, выпуск 6, сентябрь 1996 г., стр. 583–599. Ссылка
[ 13 ] А.В. Шатов, А.Е. Буров, А.В. Лопатин. «Потеря устойчивости композитной многослойной цилиндрической оболочки с решетчатым анизосетчатым заполнителем под действием гидростатического давления». 2020 Journal of Physics: Серия Конференций, сер. 1546 012139. Ссылка
[ 14 ] Дж. Гордон, «Конструкции или почему не ломаются вещи» (1978) Изд. «Мир», Москва, 1980.
[ 15 ] Васильев В.В., Разин А.Ф. «Анизосетчатые композитные решетчатые конструкции для космических и авиационных применений», Журнал «Композитные Структуры» №76, стр. 182-189. 2006.
[ 16 ] Васильев В.В., Барынин В.А., Разин А.Ф., Петроковский С.А., Халиманович В.И. «Анизогридные композитные сетчатые конструкции — разработка и применение в космической технике» Композиты и наноструктуры. 2009. №3. С. 38–50. Ссылка
[ 17 ] Васильев В.В., Разин А.Ф. «Перспективы применения сетчатых композитных конструкций в гражданской авиации» Полет. №11–12. С.3–12. 2016.
[ 18 ] Васильев В.В., Барынин В.В., Разин А.Ф. «Анизорешетчатые композитные решетчатые конструкции — разработка и применение в аэрокосмической отрасли», Журнал «Композитные Структуры» №94, стр. 1117-1127. 2012.
[ 19 ] Женг К., Джанг Д.З., Хуанг Ц.Ф., Шанг И.И., Джу С. «Анализ разрушающих нагрузок и оптимальная конструкция композитного решетчатого цилиндра при осевом сжатии», Журнал «Композитные Структуры» №131, стр. 885-894. 2015.
[ 20 ] Пауэлл К. «Геодезическая конструкция самолета». Журнал «Спортивная авиация». №8, Стр. 17–24. 1961.
[ 21 ] А.А. Прядицкий «Обзор исследований по проектированию сетчатых конструкций из композитов для авиа- и ракетостроения». УДК 629.7.023.002.3: 620.22-419 2014. Ссылка
[ 22 ] Collins, 1954
[ 23 ] Ищук М. К. «Прочность и трещиностойкость каменной кладки наружных многослойных стен». Диссертация. Москва, 2019. Ссылка
[ 24 ] Банн, В. Г. (Bunn, W. G.) «Механизм передачи сдвига сетки из углепластика / жесткой пены для сборных железобетонных многослойных стеновых панелей» диссертация, представленная на факультете выпускников Университета штата Северная Каролина, т. 1, 2011 г., стр. 8-13.
[ 25 ] Nova Cabrera, J., 2010.
[ 26 ] Т. Гарбовски, Т. Гаевски, «Определение жесткости на поперечный сдвиг многослойных панелей с гофрированным сердечником путем численной гомогенизации».
[ 27 ] Эсхан Мирнатеги, Айман С. Моссалям «Многокритериальная оптимизация энергосберегающих систем строительства из цементных сэндвич-панелей с использованием генетического алгоритма» Energies 2021, 14, 6001. doi.org/10.3390/en14186001 Ссылка
[ 28 ] Дэвис Дж. М. «Легкая сэндвич-конструкция», 2001. Ссылка
[ 29 ] Ю.Х. Мугахед Амран и др. «Инновации в дизайне, эффективность и применение конструкционных панелей с изолятором: обзор». Структуры 27 (2020) 1358–1379. Ссылка
[ 30 ] Химический энциклопедический словарь. М.: Сов. энциклопедия, 1983. С. 545.
[ 31 ] Робертс С.Б. «Сборные многослойные стены для целлюлозного завода» Engineering News-Record, V. Feb. 1951, 32-34.
[ 32 ] Комитет Сборного Бетона из Сэндвич-Панелей Института сборного/предварительно напряженного бетона (PCI). США. PCI Журнал. 1997, 63 стр. Ссылка
[ 33 ] Комитет Сборного Бетона из Сэндвич-Панелей Института сборного/предварительно напряженного бетона (PCI). США. PCI Журнал. 2011, 56, Стр. 131–176.